Polyurethane Properties and
Design Considerations
Explore the wide potential of polyurethane to solve your demanding challenges,
and then contact us to help out with design, engineering, and production.
and then contact us to help out with design, engineering, and production.
Explore the wide potential of polyurethane to solve your demanding challenges, and then contact us to help out with design, engineering, and production.
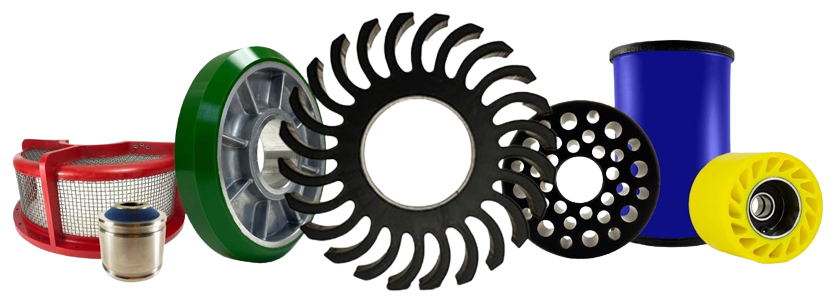
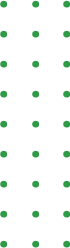
It’s a Rubber… It’s a Plastic…
It’s a Polymer
Polyurethane is all of These!
Polyurethane bridges the performance gap between rubber and plastic. Like all polymers, its performance comes from its molecular make-up. Depending on the chemistry formulation and the reaction process, polyurethane’s end-state performance is tailorable to meet exactly what you need.
Maybe you need a material that’s flexible and tough… Or perhaps you’re looking for something that is rigid yet impact resistant. Polyurethane is both (and more)! That’s why we say polyurethane is the Ultimate Engineering Material.
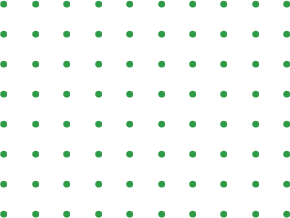
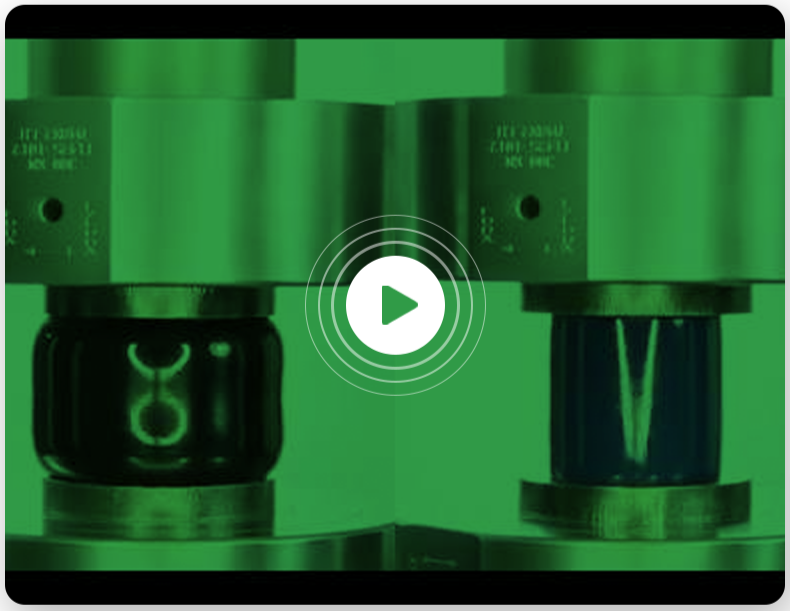
Countless Applications
Because of Three Key Advantages
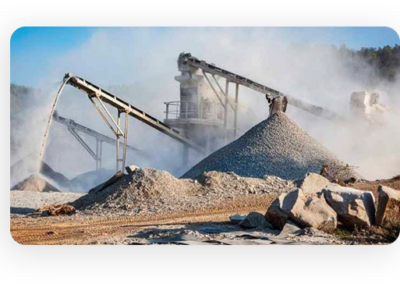
Abrasion & Wear Resistance
Polyurethanes have outstanding abrasion resistance, often outwearing corresponding parts made of metal, plastic, or rubber by a wide margin.
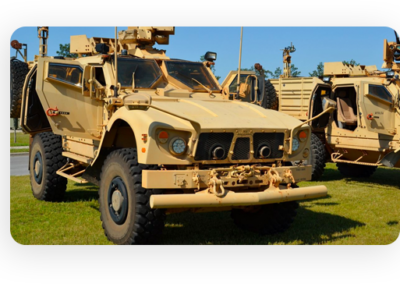
Dynamic Load Bearing and Impact Resistance
Polyurethanes have an excellent load-bearing capability and exhibit deflection and recovery that far exceed plastic or metal.
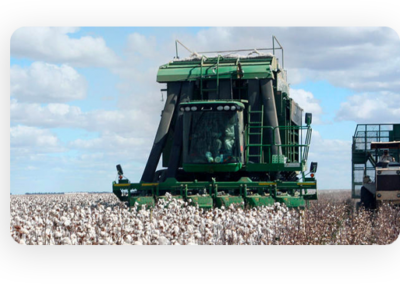
Complex Shapes & Bonding
Creating complex shapes is no problem for polyurethane because we mold it in its liquid state. Polyurethane can be permanently attached — or bonded — to metals, plastics, and composites during the molding process.
How Does Polyurethane Compare to Other Materials?
Versus Rubber, Polyurethane has
Better:
- Abrasion Resistance
- Cut and Tear Resistance
- Load-Bearing Capability
- Wear Life
Potential For:
- Complex Shapes
- Colorability
- Broader Hardness Range
- Lower Cost, Low-Pressure Tooling
Versus Plastic, Polyurethane has
Better:
- Abrasion resistance
- Load-Bearing Capability
- Impact Resistance
- Elastic Memory
- Resilience
- Compression Set Resistance
- Low Operating Temperature
Potential For:
- Complex Shapes with Thin and Thick Sections
- A variable Coefficient of Friction
- Noise Reduction
- Lower Cost, Low-Pressure Tooling
Versus Metal, Polyurethane has
Better:
- Abrasion Resistance
- Impact Resistance
- Flexibility
- Resilience
- Corrosion Resistance
Potential For:
- Weight Reduction
- Non-Conductive
- Non-Sparking
- Noise Reduction
- Lower Cost Molding vs. Metal Machining
- Lower Product Cost
We Engineer The Polyurethane To Best Suit Your Application.
What Performance Properties Are Important To You?
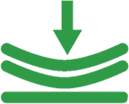
Modulus of Elasticity

Hardness
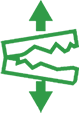
Tear Strength
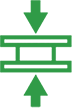
Compression Set
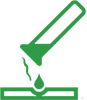
Chemical Resistance
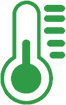
Temperature Range
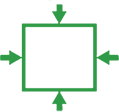
Modulus
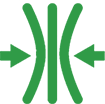
Rebound
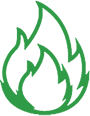
Flame Resistance
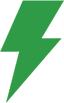
Electrical Resistivity

Food Grade
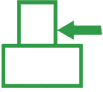
Coefficient of Friction
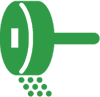
Abrasion Reistance

Colors
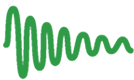
Vibration Damping
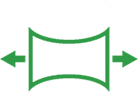
Tensile Strength
Don’t see the property you are looking for? Contact Us
There Is Even More To
Consider For Your Design
We’ll help – we understand these design considerations through and through.

Moldability

Fatigue

Hysteresis

Bonding

Dimensional Tolerances

Load Application
The Science Behind Polyurethane
This is What Makes “Amazing” Possible
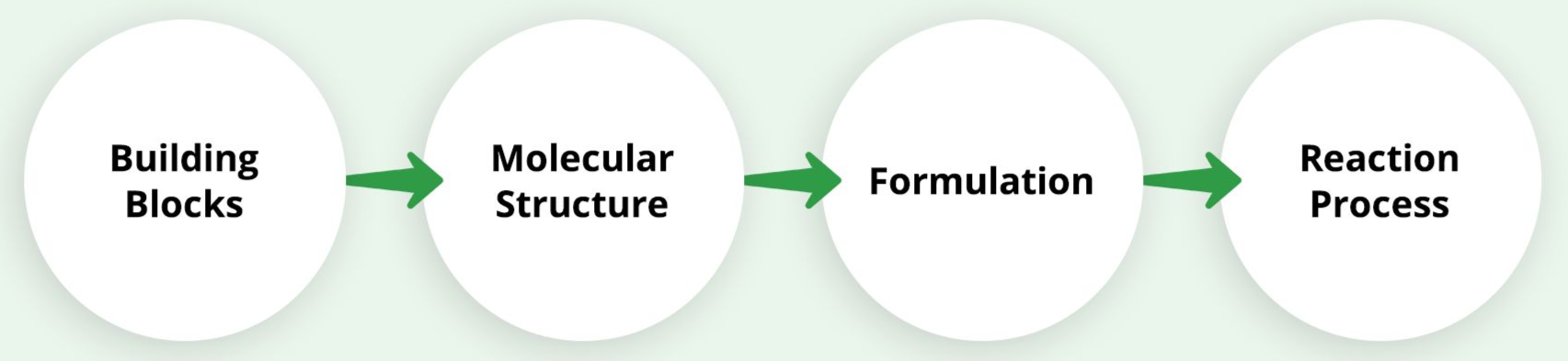