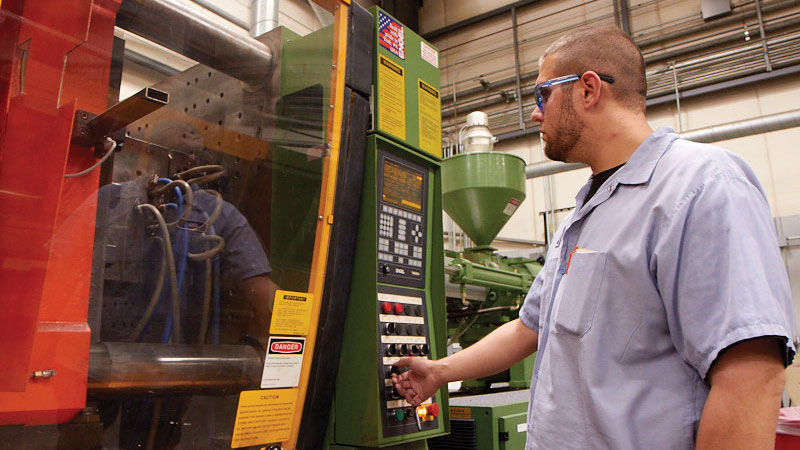
Polyurethane Injection Molding
Polyurethane injection molding stands as a cornerstone in modern manufacturing, offering unparalleled versatility and efficiency in producing high-quality components. At Gallagher Corporation, we have honed this process to perfection, delivering exceptional products that meet the diverse needs of our clients.
Understanding Polyurethane Injection Molding
Polyurethane injection molding involves injecting molten polyurethane into a precisely engineered mold under high pressure. This technique ensures the material fills every intricate detail of the mold cavity, resulting in components that are either net shape or near net shape straight from the mold. This precision minimizes the need for secondary machining, streamlining production and reducing costs.
The Gallagher Advantage in Polyurethane Injection Molding
With six decades of experience, Gallagher Corporation has established itself as a leader in polyurethane injection molding. Our advantages include:
• Advanced Machinery: Our facility houses a range of injection molding machines capable of accommodating various product sizes, from small precision parts to large, complex components.
• Complex Product Handling: We specialize in producing intricate products that may require bonding to inserts, multiple injected materials, or varying cross-sectional areas.
• Customized Material Formulations: Understanding that each application has unique requirements, we tailor our thermoplastic polyurethane formulations to meet specific performance criteria, ensuring optimal results for every project.
The Injection Molding Process at Gallagher
Our refined injection molding process encompasses several critical steps:
1. Material Preparation: Solid polyurethane pellets are fed into the injection molding machine’s barrel. A reciprocating screw within the barrel advances the pellets, generating frictional heat that melts them into a homogeneous molten state.
2. Injection Phase: Once an adequate amount of molten polyurethane accumulates, it is injected into the closed mold at high pressure through meticulously designed gates. This rapid injection ensures the mold cavity is completely filled, capturing every detail of the design.
3. Cooling and Solidification: The mold incorporates cooling channels that facilitate the uniform solidification of the polyurethane. This controlled cooling is vital for achieving the desired material properties and dimensional accuracy.
4. Ejection: After solidification, the mold opens, and the finished component is ejected using a system of pins, sleeves, or strippers. The mold then closes, and the cycle repeats, enabling high-efficiency production.
Applications and Benefits
Polyurethane injection molding is ideal for producing components that demand precision, durability, and consistency. Industries such as automotive, aerospace, medical devices, and consumer goods benefit from this process due to its ability to produce parts with complex geometries and tight tolerances.
Choosing Gallagher Corporation for your polyurethane injection molding needs ensures access to a team of experts dedicated to delivering superior products. Our commitment to quality, innovation, and customer satisfaction positions us as a trusted partner in your manufacturing endeavors.
For more information or to discuss your specific project requirements, please contact us.
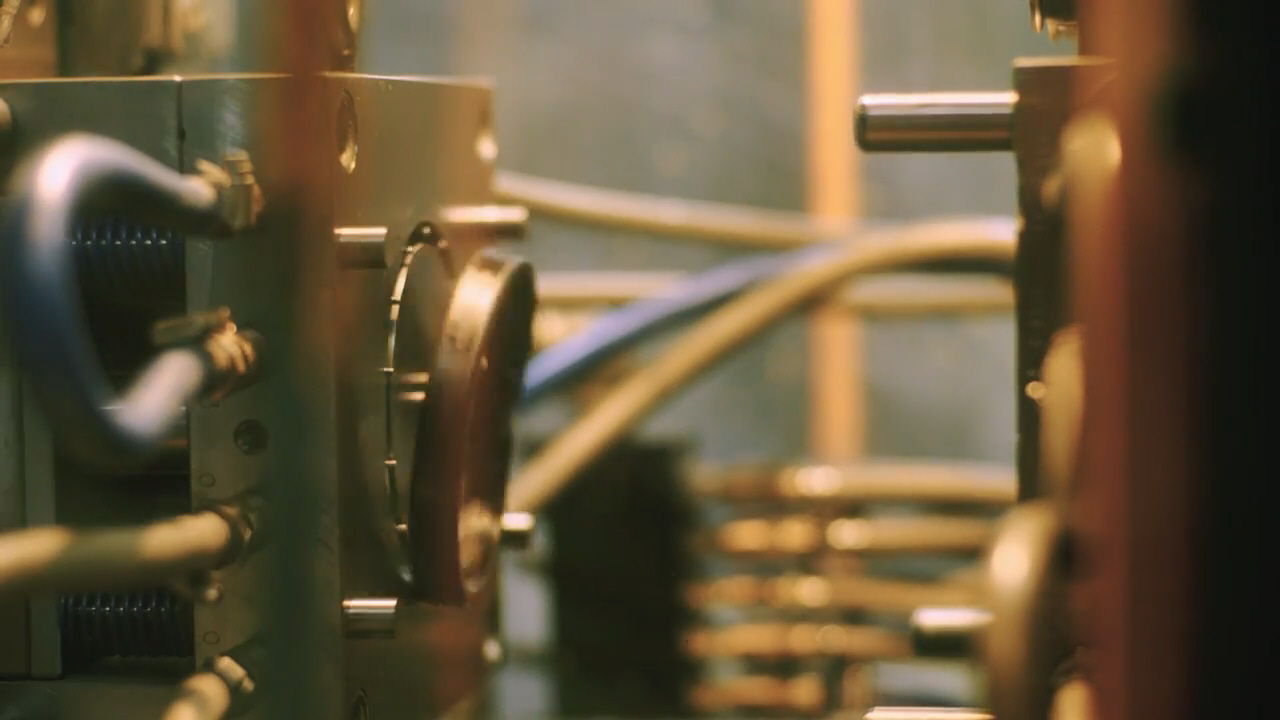