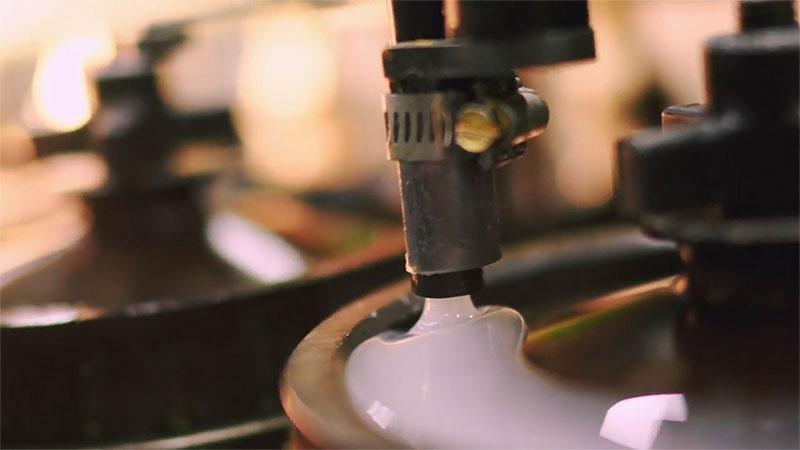
Custom Polyurethane Casting
A molding method that involves a low filling pressure and an exothermic chemical reaction
Why It Matters
Polyurethane is poured into a mold at low pressure and allowed to cure. But don’t let the straightforward process fool you.
The custom polyurethane casting process enables a tremendous amount of customization to the polyurethane’s chemistry. By customizing the polyurethane formulation, we are able to provide the best performing material for your application. Custom urethane casting also has an advantage in producing large products, or products with both thick and thin sections. These geometries are challenging for other molding methods.
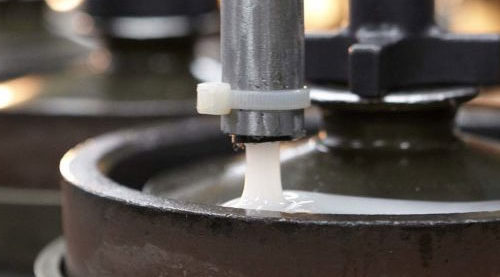
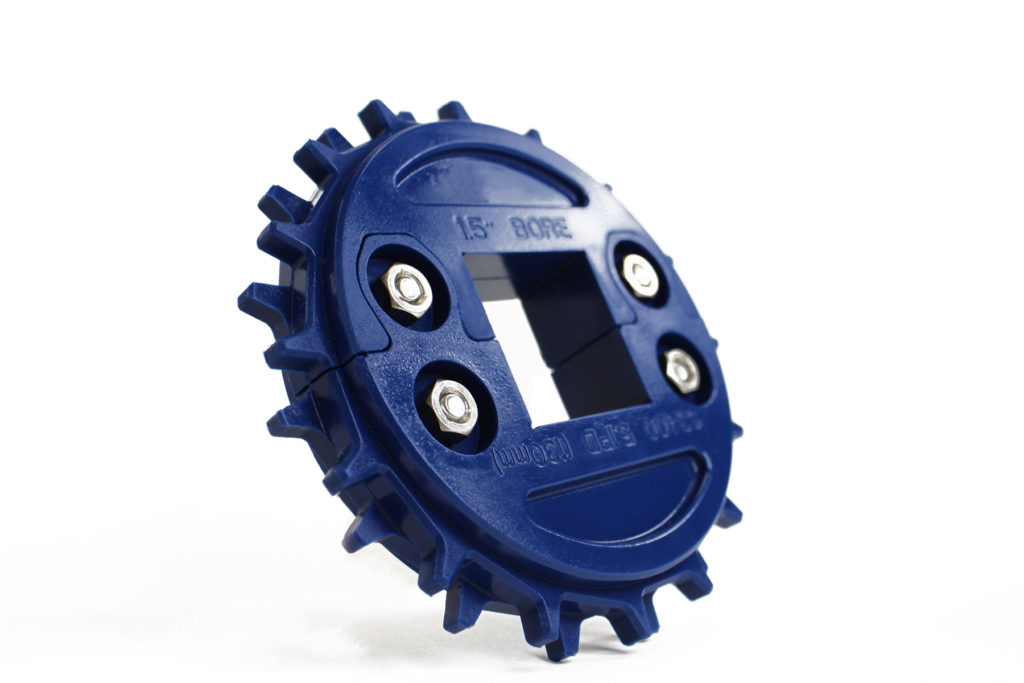
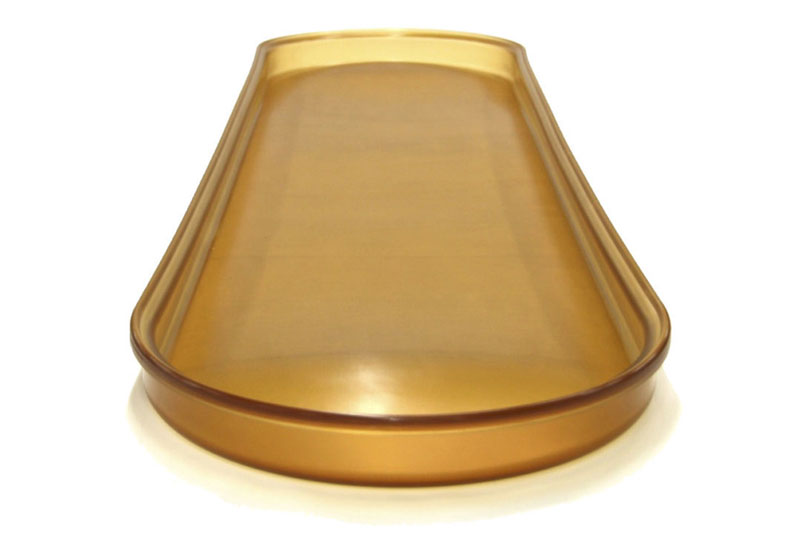
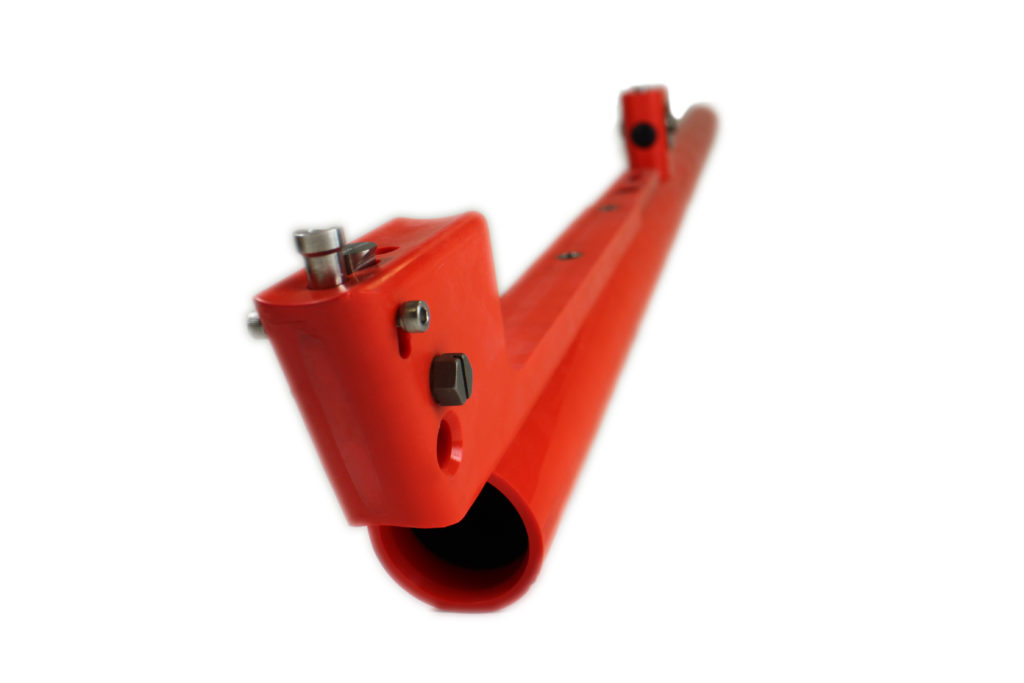
The Gallagher Advantage
We’ve been custom polyurethane casting since 1965 — so, we know a thing or two about how to achieve product quality and production throughput.
Our superior quality is predicated on precise control of the entire cast molding process, especially of the polyurethane chemical reaction that takes place. Any deviation to the process could impact the product’s dimensions or performance properties. Raw material ratios, temperature, and time are key factors of the process. We precisely control these with advanced processing equipment, automated processes, and recurring process calibrations.
We lead the cast polyurethane molding industry in using automation. It’s one way that we achieve high volume production. Our cast molding operation is competitive with injection molding.
How We Do It
At a basic level, cast molding is all about using a time-sensitive chemical reaction to cure a liquid into a solid. A chemical reaction is initiated when polyurethane’s raw ingredients are mixed together. The polyurethane mix is poured into a mold and fills all of the mold’s details before it becomes too viscous. The thermoset polyurethane cures and the solid is removed from the mold.
We take cast molding to the next level by controlling all aspects of the chemical reaction so that the solid shape is accurately formed, and so that the polyurethane takes on the desired performance properties. We precisely meter and mix polyurethane ingredients, as well as precisely control temperature and time of the polyurethane’s exothermic reaction.
There are many variations of cast molding. We consider your project aspects — like product size and shape, required dimensional tolerances, and production quantities — to determine the best molding method.
Our Common Cast Molding Methods:
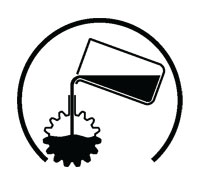
Open Cast Molding
This is the simplest of the molding methods. Polyurethane is smoothly poured into an open-top mold, or sometimes gently flowed up from the bottom of the mold. The product’s top face, or open face, usually undergoes a secondary machining operation in order to remove the over-pour.
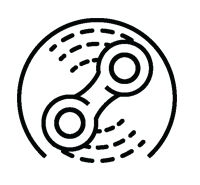
Centrifugal Molding
The mold is rotated in a horizontal plane while the polyurethane is poured in. The spinning action forces the polyurethane to move to the circumference of the mold, while the air is displaced towards the mold center. This method is used to mold products with complex details that would otherwise trap air bubbles.
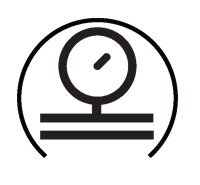
Pressure Molding
This molding takes place in a sealed chamber. The chamber is held at either high pressure or in a vacuum. This method helps to eliminate air bubbles in the finished product.
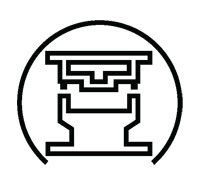
Compression and Transfer Molding
Both methods use force to clamp together two halves of a mold. The applied pressure forces the polyurethane into all cavities of the mold. This produces products with complex shapes, without the need for secondary machining operations.
Materials To Meet Your Application
Our thermoset polyurethanes cover a wide range of performance properties. We customize the formulation of our polyurethanes to meet the specific requirements of each project. Tell us about your custom polyurethane casting application, and we’ll guide you through your best material options.