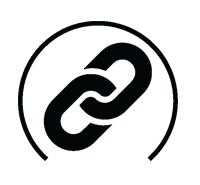
Polyurethane Bonding, Overmolding, and Insert Molding
A permanent adhesion between two materials (polyurethane and an “insert”)
Why It Matters
Bonding polyurethane to a rigid material offers design options for structural reinforcement, hybrid material construction, and/or attachment hardware. We call the rigid material an “insert.” We bond polyurethane to metal (for example, steel, stainless steel, cast iron, aluminum), plastic, and composite inserts. Some people call it polyurethane overmolding or polyurethane insert molding.
Our polyurethane bonding utilizes a chemical reaction to permanently adhere polyurethane to the insert. We can also include mechanical locking features to supplement the chemical bonding, although the added benefit of the mechanical lock is usually minimal and outweighed by the added complexity of forming the mechanical locking feature.
With our chemical bonding process, we achieve bonds that are stronger than the polyurethane itself. What does “bonds that are stronger than polyurethane” look like? If the polyurethane were to be forcibly pulled from the insert, then the polyurethane would tear within its bulk instead of cleanly separating at the bond line.
Polyurethane bonding can be a critical consideration for applications like wheels (polyurethane tread bonded to a metal hub), bumpers/pads (attachment bolts bonded into the polyurethane), and bushings (polyurethane bonded to a metal core or metal sleeve).
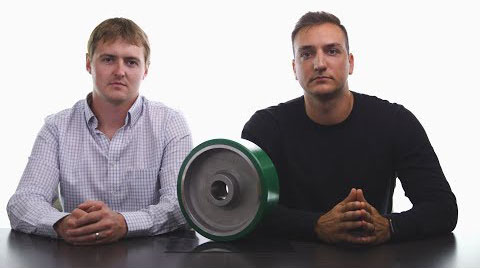
The Gallagher Advantage
A majority of the parts that we manufacture include some aspect of polyurethane bonding. Rest assured that overmolding is a skill that we employ daily. Our training, production, and inspection methods and processes are robust.
We precisely control our polyurethane overmolding process to ensure bond quality and strength. We measure and control parameters like time, temperature, surface cleanliness and surface finish, and dry film thickness to create optimal conditions for polyurethane bonding. Preventing contamination is also critical. We emphasize strict process controls because we have found that is the best way to guarantee great bonding.
We verify the quality and strength of our polyurethane bonding by performing non-destructive or destructive testing. Depending on requirements, non-destructive testing can be completed on all or a sample of production parts. Of course, destructive testing can only be completed on a sample of parts. Destructive tests measure bond strength by physically separating the polyurethane from the insert. Destructive testing is the most objective gauge.
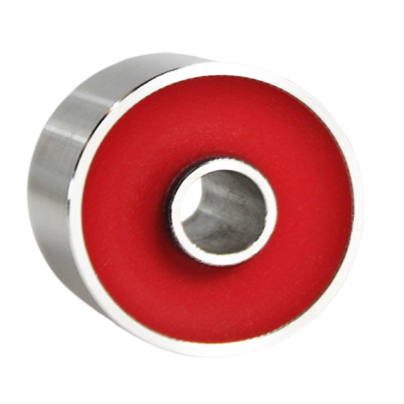
How We Do It
Preparation
Cleanliness is the foundation of our polyurethane bonding process because contaminants – like oil, grease, oxidation, or even skin oils – will prevent strong chemical bonds from forming. We have a variety of washing techniques (for example, cabinet, in-line) to accommodate a wide range of insert sizes and geometries.
An insert’s surface finish will also impact bond strength. The right surface texture creates an anchor pattern which adds an additional, and helpful, element of shear to the bond interface. The anchor pattern also increases the bonded surface area between the insert and the polyurethane. It is important that the blasted surface’s roughness is neither too smooth nor too rough, as either condition will degrade bond strength. We perform abrasive grit blasting to achieve optimal surface roughness. We have a variety of blasting techniques (for example, tumble, index, manual) and blasting media to accommodate a wide range of insert materials, sizes and geometries.
Priming refers to the application of a chemical bonding agent to the insert. The bonding agent acts as a transitional reactant between the insert’s surface and the polyurethane. A uniform and precise primer thickness contributes to optimal bond strength. We have a variety of priming techniques (for example, spray, brush, dip) to accommodate a wide range of insert sizes and geometries.
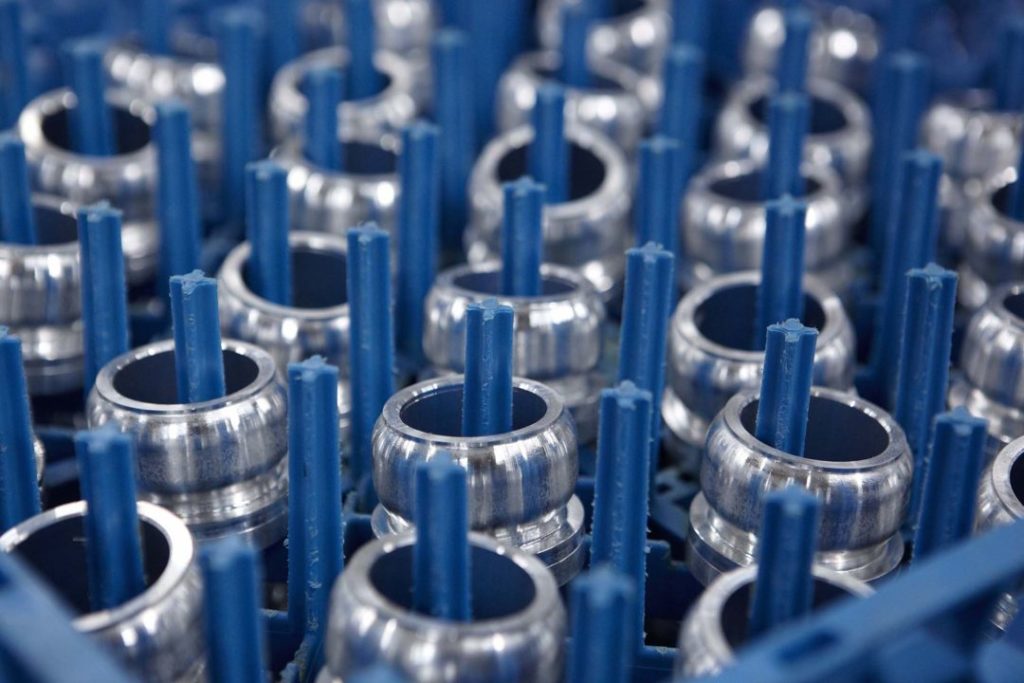
Bonding
- The reaction process begins by pre-heating the primed insert. This activates the bonding agent, bonds it to the insert, and readies it to react with the polyurethane during the subsequent molding operation.
During molding, as the liquid polyurethane cures, it reacts with the primer to fully adhere to the insert. When complete, the polyurethane bonding will be stronger than the polyurethane itself.
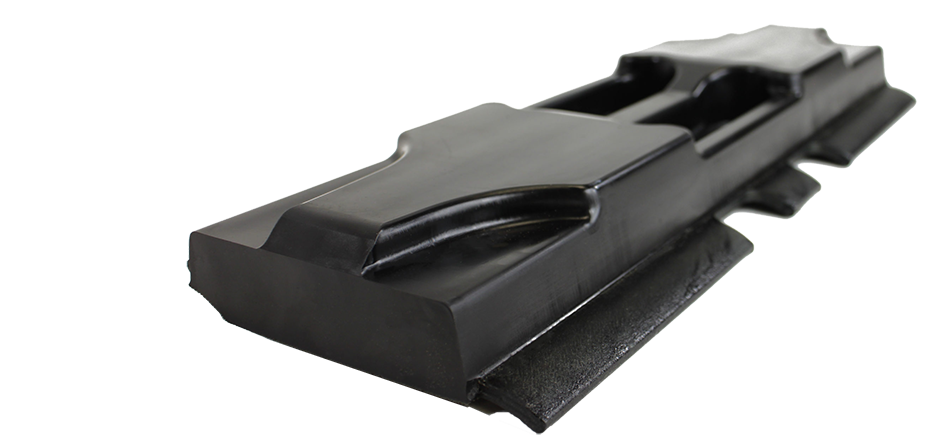
Testing
We verify the quality and strength of our polyurethane bonding by performing non-destructive or destructive testing.
- Visual inspection of the bond can be sufficient for some products.
On the other hand, some products may require that the bond strength be confirmed using special tests. Depending on requirements, non-destructive testing can be completed on all or a sample of production parts. Of course, destructive testing can only be completed on a sample of parts. Destructive tests measure bond strength by physically separating the polyurethane from the insert. The most common test that we do is a peel test, which measures the pull force required to separate the polyurethane from the insert. We also regularly do a shear test, where we apply shear stress to the bond line and evaluate for any separation. Destructive testing is the most objective gauge.
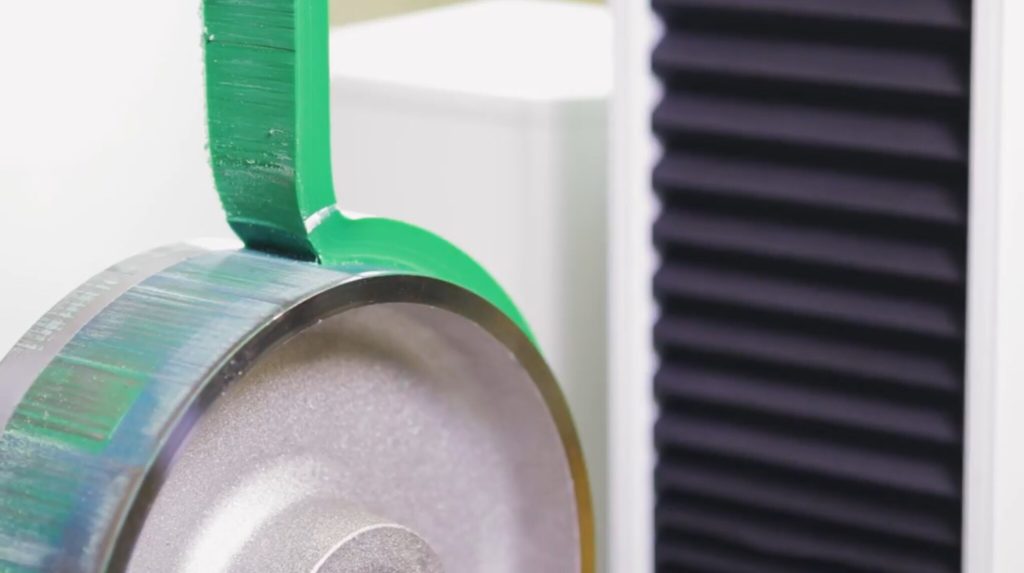
Key Takeaways
Polyurethane bonding offers useful product design possibilities.
We achieve bonds that are stronger than polyurethane itself.
We precisely control our bonding process to ensure bond quality and strength.
Your Next Step
You have found the right people (us!) if strong polyurethane bonding is critical to your product. Take a moment to rejoice that your search is finally over. Now book a quick 15-minute introductory meeting with us using the below scheduling app.
Still want to nerd out some more? Go ahead; there is plenty more to our Design Guide. We are engineers too, so we get it. But before you do that, don’t delay on the introductory meeting — it will literally save you time and jump-start your project.