Machining Cast Polyurethanes
Cast polyurethanes can be readily turned, waterjet cut, sawed, drilled, ground or milled. We offer many engineering shapes of our compounds which can often be used to make prototypes or limited production quantities. It is important to note that the material presented here is a starting point. The wide variety of urethane compounds and their respective physical properties and characteristics creates a wide range of situations.
Harder urethanes – 90A and up – have a high degree of machinability. Lathe turning, fly-cutting, grinding, contouring and more are easily accomplished on conventional metal working equipment by machinists who are familiar with procedures for handling plastics.
Some different tools and techniques are required for compounds of 80A durometer and lower. These lower modulus compounds are typically machined by knifing, grinding or sanding. However, in some cases, they can be worked like higher modulus materials by “freezing” them with dry ice or liquid nitrogen.
Key Points to Remember When Machining Polyurethane
Thermal Conductivity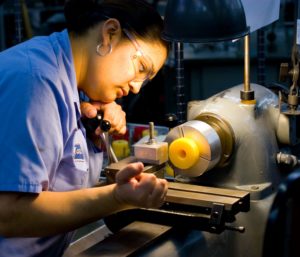
Urethanes have much lower thermal conductivity than metals, so heat generated by cutting tools stays close to the tool and raises the
urethane surface temperature rapidly. This heat must be controlled. Melting can occur above 350ºF (175ºC). In addition to possible melting, heat generated by machining causes the part to reversibly expand. When the part cools, it shrinks and could become undersized.
Elastic Memory
Elastic recovery occurs in urethane both during and after machining. The cutting tool must provide clearance to compensate for this. Without compensation, expansion of the urethane as it passes the tool will result in increased friction between the cut surface and the cutting tool. Excess heat build-up will result. Elastic recovery after machining can result in smaller internal diameters and larger external diameters than were measured during cutting.
Modulus of Elasticity
Urethanes are compliant and can easily be distorted. It is possible to alter the shape of a urethane part by clamping or chucking it with too much force. This would cause the final machined shape to be distorted after the cuts have been made and the fixturing pressure was released. Care must be taken to hold parts securely, but to avoid distortion due to holding or cutting.
Softening Point
Gumming, poor finishes, and poor dimensional control will occur if excess heat is generated and allowed to accumulate. Proper tool geometry, feed rates, and cutting speed, in conjunction with coolants usually will overcome these problems. Water soluble cutting oils and/or light machining oils are good coolants for urethanes.
GENERAL SAFETY CONSIDERATIONS
When performing any machining or other secondary operations on urethanes, we recommend that all appropriate safety equipment, as well as personal protective devices be utilized at all times.
Eye protection should consist of approved safety glasses with side shields or full goggles. A full face shield is recommended whenever chip pieces or work pieces could fly out and strike the operator in the face.
Fixturing is an extremely important aspect of machining urethane. Never attempt to start machining until you are positive that the fixturing is safe and secure. Improper fixturing during plunge cuts and contouring can cause the work-piece to come out of the machine and injure the operator or a bystander.
CAUTION! Excessive heat can be generated by improper machining practices. If smoke is generated, the method must be immediately corrected. DO NOT inhale the smoke or grinding dust from urethane or any elastomer or plastic.