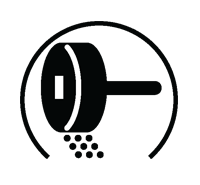
Polyurethane’s Abrasion Resistance
The ability to withstand wear typically caused by mechanical action
Why It Matters
Polyurethane’s abrasion resistance is a key performance advantage of polyurethane. It’s why you find polyurethane used in so many applications that experience high wear. Examples include bushings, bearings, wheels, sprockets, and wear liners. More examples ›
Polyurethane withstands the typical forms of abrasion: sliding, impingement, and slurry. It resists the tearing associated with sliding abrasion. And it absorbs and recovers from the particle impacts associated with impingement and slurry abrasion. Some applications will present a mix of these abrasion types.
Sliding Abrasion
Sliding abrasion occurs when one surface slides over another – also called two-body abrasion. Or sliding abrasion occurs between two surfaces separated by dry particles or slurry – also called three-body abrasion. In both, localized areas of high strain occur at the interface and create minute tears in the surface. Polyurethane with a low coefficient of friction and a high tear strength resists sliding abrasion.
Impingement and Slurry Abrasion
Impingement and slurry abrasion occur when particles impact a surface. Particle trajectories can range from perpendicular to grazing angles. The particle impacts cause localized areas of high strain and break off minute sections of the surface. A resilient polyurethane compound is ideal for impingement and slurry abrasion applications. It will absorb the energy of the particle impacts, distribute the stresses, and then recover with little or no damage to its surface.
Polyurethane’s abrasion resistance is dependent on a combination of basic properties such as tear strength and resilience, which result from the polyurethane’s formulation. We can tailor the abrasion resistance of polyurethane to fit your specific application.
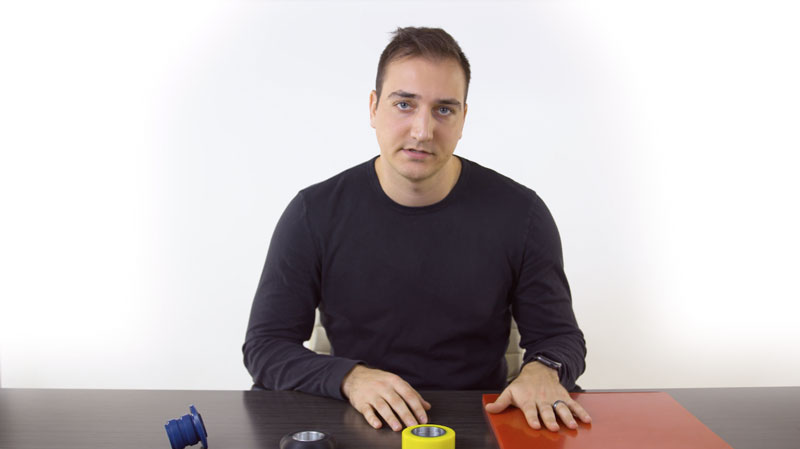
Measurement
Polyurethane’s abrasion resistance is typically measured in units of mass or volume loss, or as a percentage thereof.
We select the best test method based on the nature of the intended application. Even then, a correlation between test results and service performance is often quite difficult to establish. Tests generally accelerate wear rates to make testing durations more practical. But in the field, the same components would be gradually worn over a long period of time. The accelerated wear rates of tests generate extra heat that is not representative of the operation. Heat build-up within polyurethane reduces its performance. Therefore, abrasion tests are more useful for comparing materials than for predicting polyurethane’s in-service performance.
Sliding Abrasion
There are many widely accepted ASTM tests for measuring polyurethane’s resistance to sliding abrasion. In each test method, the abrasive action is applied for a specified duration and under a specified force.
- ASTM D1630 — Standard Test Method for Rubber Property – Abrasion Resistance (Footwear Abrader) — sometimes referred to as the NBS test. This test measures two-body abrasion.
- ASTM D5963 — Standard Test Method for Rubber Property – Abrasion Resistance (Rotary Drum Abrader) — sometimes referred to as the DIN test. This test measures two-body abrasion.
- ASTM G65 — Standard Test Method for Measuring Abrasion Using the Dry Sand/Rubber Wheel Apparatus. This test measures three-body abrasion.
- ASTM G105— Standard Test Method for Conducting Wet Sand/Rubber Wheel Abrasion Tests. This test measures three-body abrasion.
Impingement and Slurry Abrasion
On the other hand, there are no specific ASTM tests used to measure polyurethane’s resistance to impingement and slurry abrasion. Instead, we test these abrasion types using in-house test methods and equipment that are application-specific.
Typical Values
Polyurethane often outwears corresponding components made of metal, plastic, or rubber by a wide margin. But its superior performance in an application is only achieved by selecting the optimal formulation. We engineer the polyurethane’s properties for your specific application.
An example can illustrate the benefit of matching properties to the application. This application incurs sliding abrasion from dry, rounded quartz aggregate. Therefore, we select the ASTM G65 test to compare materials. Of the four materials tested, the polyester-based polyurethane shows the best abrasion resistance. It shows just slightly better abrasion resistance than D2 tool steel. And it’s clearly better than ultra-high molecular weight polyethylene (UHMW PE), or a polyether-based polyurethane with higher hardness. For the specific conditions tested, the polyester-based polyurethane has the optimal mix of properties.
A different application, for example, one with slurry abrasion, would require a different test and would likely benefit from a different polyurethane formulation.